Innovations developed within the BiDebA project paved the way for more sustainable and repairable composite poducts. Developing adhesives that are both biobased and debondable on command, it provided a significant contribution to circularity in crucial industries such as aerospace, automotive, and construction, where strong, lightweight, and easily repairable bonds are essential.
Read more about our innovative research on smart debonding solutions in this blogpost.
Innovations in debondable adhesives like those developed in BiDebA will play a pivotal role, ensuring components are efficiently repaired, reused, or recycled."
The Importance of Debonding
Adhesive bonding is widely used, but it creates challenges when components need to be repaired, reused, or recycled. Traditional adhesives are fossil-based and difficult to remove without damaging the substrate.
Debondable adhesives offer a smarter solution: they maintain strong bonds during use but can be selectively weakened—typically by heat—when separation is needed. By using biobased adhesives also, the carbon footprint can be reduced.
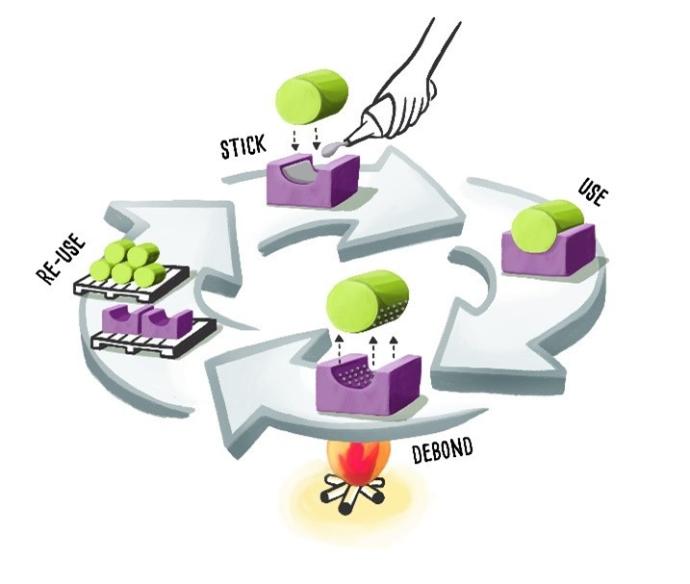
Aerospace Application:
Quick Composite Repairs
A primary use case explored by BiDebA is Quick Composite Repair (QCR) for aircraft engine cowlings. These composite structures can be compromised by hail, bird strikes, or debris. Current QCR practices typically employ permanent adhesives such as epoxy, complicating the removal of temporary repair patches and often risking damage to the original structure. Such processes are labor-intensive, costly, and slow.
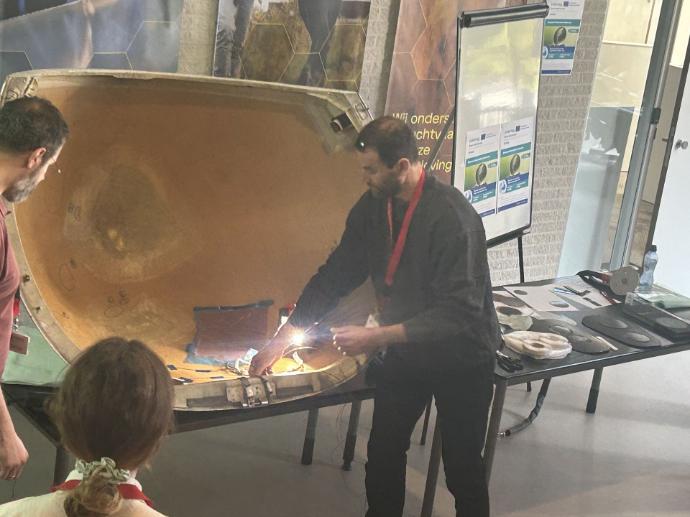
By contrast, biobased thermally debondable adhesives streamline this process. The patches applied using these adhesives can be swiftly and safely detached using heat, significantly reducing repair times and minimizing risks of structural damage, aligning seamlessly with broader sustainability objectives.
Smart Adhesive Solutions
Evaluating Biobased Adhesives
Two biobased adhesives were evaluated within the project:
Copal Tree Resin: A thermosetting adhesive with moderate shear strength (~1.4 MPa) debonding between 85–134°C.
Polylactic Acid (PLA): A renewable thermoplastic derived from corn or sugarcane, exhibiting superior mechanical strength (~22 MPa shear strength) with clean debonding at temperatures between 145–154°C.
PLA emerged as the most promising candidate, balancing high performance with efficient debonding.
Debonding Technologies Explored
The project investigated several innovative debonding methods:
- Induction Heating was inspired by archaeological adhesives that used iron-rich additives like hematite. Researchers added hematite to PLA to enable magnetic heating, but tests showed minimal temperature increase—indicating the need for further material optimization.
- Expandable additives such as Thermally Expandable Particles (TEPs) and graphite were tested to create internal pressure during heating and hence allow easy detachment. Some showed promise, but finetuning of the particles with the adhesive matrix is needed as theoretical data in datasheets is not always matching reality. Additionally, the method remains more expensive and complex than simply heating. Biobased variants like Expancel BIO offer a sustainable path forward if technical challenges can be resolved.
- Thermal Debonding via convection proved the most effective. Heating the adhesive (e.g., with a heat gun) softens it, allowing for clean separation without damaging the substrate. This method is practical, scalable, and ideal for field repairs.
In Conclusion: A Circular Future for Composite Bonding
The BiDebA project demonstrates that biobased adhesives, notably PLA, can be strategically designed for both high strength and intelligent debonding capabilities. While thermal debonding via convection currently represents the most viable solution, continued research into induction heating and expandable particles holds promise for future enhancements.
As industries increasingly adopt circular design principles, innovations in debondable adhesives like those developed in BiDebA will play a pivotal role, ensuring components are efficiently repaired, reused, or recycled, ultimately fostering a more sustainable industrial ecosystem.