Start writing here...
GMI Aero's collaboration in the BiDebA project promotes a circular approach to aircraft maintenance. They are combining new, bio-based adhesives with their smart heating technology. The goal of this innovative apprach? Cutting costs, saving time, and advancing sustainability in aviation.
The goal: Circular Economy
Aligning with the circular economy's waste hierarchy principles, extending the lifespan of composites through repair and reuse is crucial. The major challenge lies in the inextricable bonding of composite materials through adhesives. Conventional adhesives exhibit a two-fold challenge:
- They are primarily produced from fossil fuels and are therefore non-renewable.
- Once applied, they cannot be easily detached and hinder further repair, reuse, and recycling.
BiDebA aims to tackle this challenge by creating bio-based adhesives from renewable resources that can hold firmly when needed—but also release cleanly and on command, allowing for more efficient, circular repair processes.
North-West Europe is home to the largest share of the European composite and adhesive market and the transportation sector, the largest consumer of composites. That is why the project includes companies involved in composite repair. Via demonstrations we can convince companies to adopt these technologies in their products and processes.
Composite Repair in Aeronautics
When every minute counts
Aircraft today rely heavily on lightweight composite materials. But when damage occurs—from hail, impacts, or everyday wear and tear—repairing those composites can be slow and complex. Unscheduled repairs are especially costly: keeping an aircraft on the ground can cost up to $100,000 per day in lost revenue. On top of that, many repairs require special materials and highly trained technicians.
It’s easy to see why airlines need quick and reliable repair solutions...
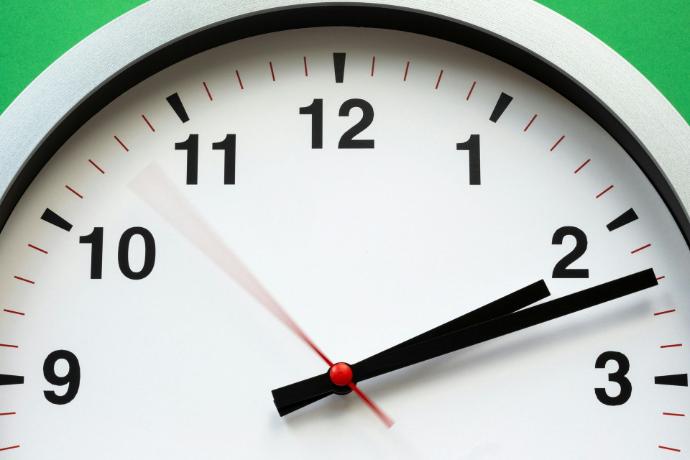
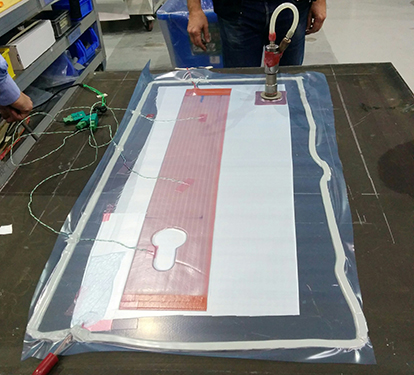
Quick Composite patch Repair...
GMI has already developed a practical answer: the Quick Composite Repair (QCR) heating blanket. This low-cost, easy-to-use tool allows technicians to apply a repair patch to small areas of non-critical damage—sometimes within just one hour. Crucially, this type of repair doesn’t require extensive disassembly, hazardous equipment, or high-level composite expertise.
...made Smart and Sustainable
Through the BiDebA project, we are now enhancing our QCR technology with new bio-based adhesives that are not only derived from renewable sources but also designed to be easily removed. That means temporary patches can be taken off cleanly when a permanent repair becomes possible, without the time-consuming and damaging removal process that traditional adhesives require.
This combination of fast-heating technology and smart adhesives has two key advantages:
Economic: Quicker repairs mean less aircraft downtime and fewer delays. Plus, they can be applied by general maintenance staff, reducing the need for specialized composite technicians.
Sustainable: The bio-based adhesives support the circular economy by being recyclable, renewable, and easy to remove—making future repairs and recycling easier.
Looking Ahead
With the transportation sector—and aviation in particular—facing growing pressure to reduce environmental impact, projects like BiDebA are a crucial step forward. By making composite repairs faster, smarter, and more sustainable, we can help airlines cut costs, reduce waste, and get aircraft back in the sky faster.